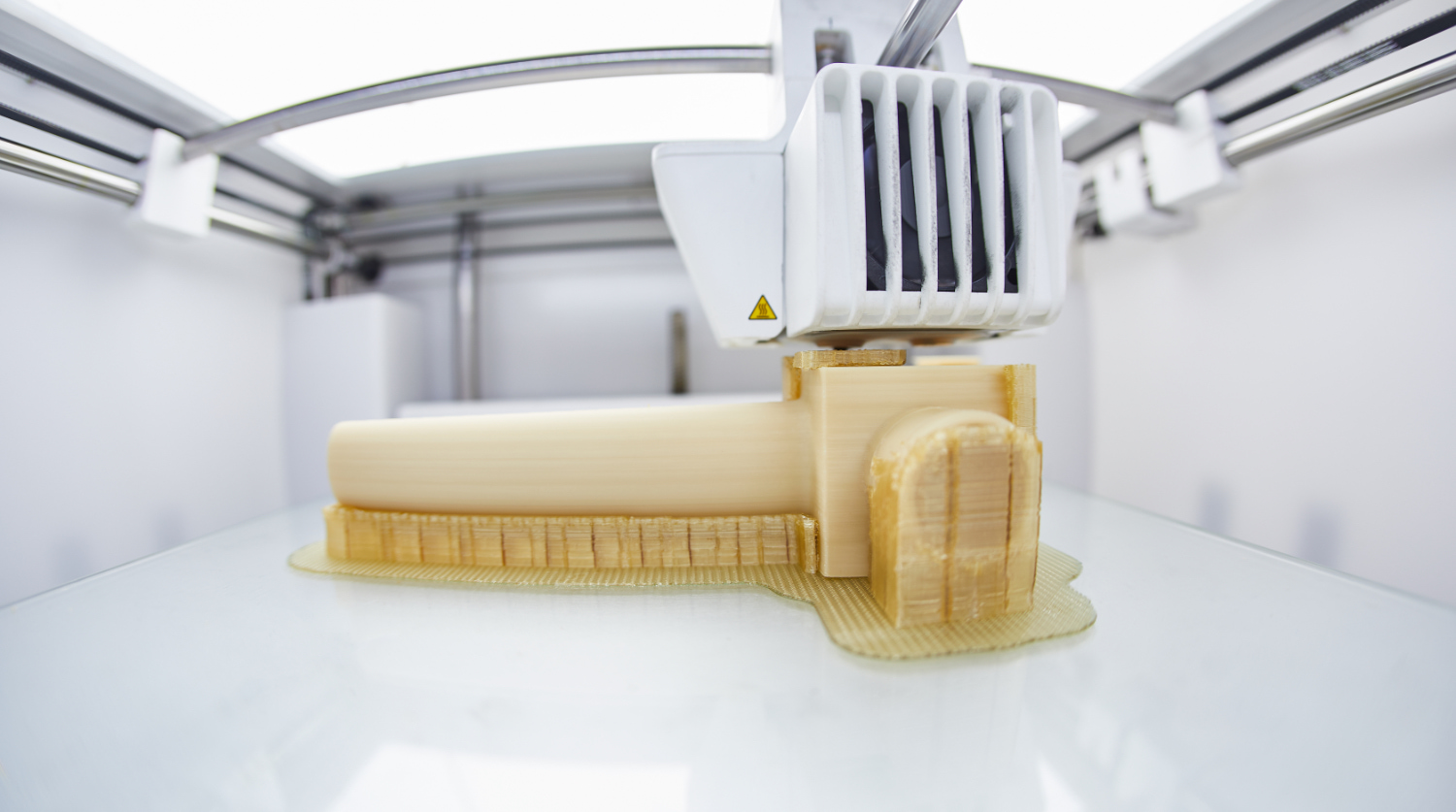
Words You Need to Know
Additive manufacturing terminology
Let's speak the same language. Here are some important 3D printing definitions and additive manufacturing terms you need to know.
- Industry Terms
- Parts & Process
- Materials
Industry terms.
A manufactured product that's ready to market.
A type of additive manufacturing technology where a part is constructed by adding one layer of production-grade thermoplastics on another. FDM uses industrial-grade materials to create strong, durable, detailed end-use parts and prototypes.
A type of additive manufacturing technology used to build 3D models. With FFF, one layer of molten plastic is added onto another to create a product or model. FFF is often used interchangeably with FDM.
A jig is a tool used to guide a machining tool; it essentially controls the motion or location of another tool. A fixture is a tool that ensures the position of a tool; it essentially acts as a support device.
The degree of exactness and similarity between two printed parts in terms of dimensional tolerance and surface finish.
The quick fabrication of a product, model, or part that's enabled through 3D computer aided design (CAD). In rapid prototyping, the part or model is typically created by additive manufacturing.
The ability of a polymer to resist heat and degradation.
Parts & processes.
Support material that is manually removed after printing.
Similar to a raft, a brim is a mesh material substrate. The raft is placed around the 3D object being built, essentially creating a protective skirt to prevent the edges of the part from curling while adding additional material to hold the part down.
Materials used in additive manufacturing to create 3D products and prototypes.
The area where the 3D print is actually printed on.
The inability (or limited ability) to configure the equipment and design capabilities based on the project or user need.
3D printing systems that have a limited choice of material and don't provide a software choice. Closed systems only work with a permanent supplier and a fixed temperature.
The process of using composites (engineered materials made from two materials with different physical or chemical properties) to create tools that will be used in manufacturing.
Specific printing parameters according to personal/company design and order.
The act of dissolving a material.
A component of the 3D printer that ejects materials that have been heated to liquid form into layers for 3D printing. A single extruder system prints one filament at a time, which offers simplicity and ease of cleaning. A dual extruder system prints two filaments at a time, including support material, which offers greater printing diversity but increases cost. A multiple extruder system prints several filaments at a time.
The route the filament takes from the spool to print head, mostly commonly through PTFE tubing.
A sealed, insulated enclosure that helps to reduce cooling and contain fumes from materials.
A component of the 3D printer that melts down the filament so it can be pushed through the extruder. A hot end helps keep the filament at an optimal temperature and consistency. A hot end is synonymous with liquifier.
The material that occupies the internal part of an object. The infill influences the object’s weight, strength, and structure. Sparse infill requires plastic to be extruded as a scaffolded layer rather than layer upon layer, as is the case with solid infill. Sparse infill is used to lighten the weight of the product or part. Dense infill means a lot of plastic has been added to the part to increase the object's strength.
A repeated design of infill to improve an object's strength, flexibility, or aesthetics. A linear pattern is where only one axis is printed per layer to produce a 2D grid. A gyroid pattern is a 3D pattern resembling waves and has equal thickness in several directions to give it the ability to provide support in every direction of the object. A zig-zag pattern is a grid-shape design that prints continuously in one diagonal direction back and forth.
The bonding of each successive layer printed on top of the previous layer. Proper layer adhesion is vital to ensure that final part doesn't split or separate.
A component of the 3D printer that melts the polymer so it can be pushed through the extruder. A liquifier is synonymous with hot end.
When printing with multiple materials, print profiles may need be developed to optimize the interactions between build and support materials.
A measurement of the resistance to deformation of a solid material at a specific temperature.
Water-soluble supports are inherently sensitive to moisture and will absorb moisture over time when exposed to high humidity. Too much moisture will have a negative impact on printing. Keeping material in a sealed dry place, such as a sealable foil bag, or desiccant box, will ensure fewer issues when printing.
The ability to configure the equipment and design capabilities based on the project or user need.
3D printing systems that promote free choice in materials and suppliers. Open systems are compatible with all 3D software and allow for an adjustable temperature range.
The last stage of the additive manufacturing process where the final touches like painting, sanding, and support removal are completed.
A motorized heated syringe that directs the melted filament along the desired path.
The purge process is used to clean out a machine. For example: using material to push out degraded polymer from a hot end.
A hollow cylinder created on the build plate made to the height of the component desired. The purge tower cleans excess material off the nozzle before continuing the printing process.
A sacrificial structure printed as the first few layers of a build. The purpose is to create a perfectly level platform to correct for build plate imperfections and to provide an alternative substrate to adhere to when materials aren't sticking.
A software application used for the conversion of digital 3D models into printing instructions for a given 3D printer to build an object.
A core made of water-dissolvable material.
Support material that dissolves in water, thereby eliminating the need to remove manually.
Material that enables a complex 3D design to print successfully. Support is the extra material needed during the print process, but it is then discarded during post processing.
The time it takes to design, prototype, and finish a product or model.
The shrinking or curling of printing materials along the object’s lateral surfaces, most commonly at the corners. Warping and curling is a common problem that happens during cooling, or if the material hasn't been properly adhered to the build platform.
Materials.
A natural-colored water soluble filament material that performs well adhering to ABS and PLA but is incompatible with engineering-grade build materials, as well as PEEK, PEKK, PEI, and PPSU. BVOH has a higher solubility than PVA but is similar in that it requires minimal post processing, enables complex geometries, and is not stable at high temperatures.
Strong, versatile material with great thermal resistance and chemical resistance. A great material for printing mechanical parts. CPE is also used for printing large objects because it has almost no warping.
A popular material in the plastics industry known for its toughness and flexibility. Nylon filaments typically require extruder temperatures near 250ºC, however, some brands allow printing at temperatures as low as 220ºC due to their chemical composition.
A thermoplastic known for its incredible strength and impact resistance. The basis of bulletproof glass, polycarbonate is lightweight and exhibits a translucency that is superior to other Fused Filament Fabrication (FFF) 3D printing materials. Polycarbonate offers heat resistance, is flame-retardant, and insulates electricity, making it essential to use in electrical components and hardware.
A tough material designed for strong, resilient parts. This unique material provides vast improvements (over standard acrylonitrile butadiene styrene or ABS) in heat deflection, impact resistance, rigidity, and surface finish. PC/ABS is a blend of polycarbonate and ABS plastic, which combines the strength of PC with the flexibility of ABS.
A semi-crystalline thermoplastic known for its excellent mechanical strength and chemical resistance. PEEK is created by a step-growth polymerization process conducted at very high temperatures.
3D printed variant similar to PEEK material that operates much the same way as PEEK. Unlike PEEK, PEKK displays both amorphous and crystalline material properties.
A great building surface for any 3D printer. The amber-colored surface is commonly used to print a wide range of different filament types, including two of the most commonly used ones, ABS and PLA. PEI is widely becoming the gold-standard build surface because it's convenient to use. PEI is also the most commonly used material in the aerospace industry due to its VO flame performance and no smoke generation.
A thermoplastic made from renewable resources such as corn starch, tapioca roots, or sugar cane. Due to its ecological origins, this material has become popular within the 3D printing industry and is being used in medical applications and food products.
High-performance thermoplastic in the PSU (polysulfone) family. Polysulfones describes polymers containing a sulfonyl (O=S=O) moiety in their repeat unit. These thermoplastics are often used in specialty applications as a superior replacement for polycarbonates. Other polymers from the same family include PSU polysulfone(PSU), polyphenyl sulfide (PPS), and PSF poly (bisphenol-A sulfone).
One of the most common polymers found around the house. PP is great for its translucency as well as its resistance against chemicals and fatigue. Being both food- and microwave-safe, it’s often used in household plastic containers. For 3D printing, PP is also great for anything that needs to be light, water-tight, or durable. Case hinges, for example, represent a very popular use, as PP can bend repeatedly without breaking.
A white-colored high-tensile synthetic polymer filament. PVA is water soluble but incompatible with engineering-grade build materials, as well as ABS, PC, PEEK, PEKK, PEI, and PPSU. While it requires minimal post processing and enables complex geometries, PVA is not stable at high temperatures.
Referred to as the bridge between rubbers and plastics. The material appears rubber-like, which means it can be extremely flexible, durable, and smooth to the touch. All these properties and compound versatility make TPU widely used in many industries for coatings, components, and customer goods. It is often used for 3D printing.