The critical role of 3D printing support material
By Infinite Editorial Team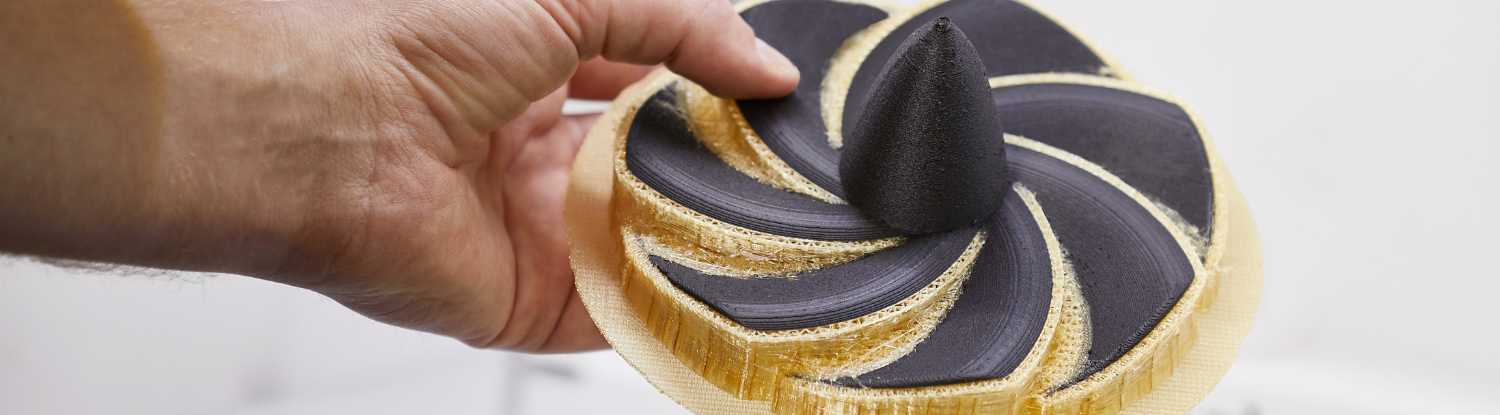
Get to know your supporting partner in additive manufacturing
Unless your goals are limited to custom hockey pucks and little gnome figures, support materials will play a critical role in your 3D printing efforts. 3D printing support materials enable you to create and print complex geometries, parts with internal features, and parts that cannot be manufactured by any other method. Without support, your build material would deform before it hardened.
Just as there are many build material options available, such is the case for support materials; and compatibility between build and support material is only one consideration. Here's a look at the different categories, and other factors that can impact which materials you choose.
Breakaway vs. soluble support materials
Printing support material is removed either physically, as in the case of breakaway materials, or dissolved with soluble support. Breakaway support is trimmed, sanded, or otherwise mechanically removed. Depending on the build material and shape of the printed object, removing support may be simple or laborious. Delicate details can make removal difficult without damaging the print, and complex voids or other internal structures simply aren’t possible at all with breakaway support. This is where soluble support comes in.
Soluble support is removed by placing the printed object in a bath of water or solvent. Dissolution rates vary widely depending on material, temperature, and if additional mechanical agitation is used. Solvent-based supports can perform well but can pose environmental hazards and health risks.
Water-soluble support material
Water-soluble support frees users from the drawbacks of breakaway support and the hazards of solvent-based support removal. The creation of well-performing water-soluble support material was pursued by many in the industry, but it posed a formidable technical challenge.

Many water-soluble polymers are too brittle to render into water-soluble filaments. Plasticizing could solve that issue, but in turn, it can inhibit thermal stability and adhesion properties. Additionally, a limited number of commercially available resins are truly water-soluble.
Today, many water-soluble 3D printing filament options are out there, including acrylate terpolymers-based (ATP) polymers, a sub-class of soluble support requiring an activator to create an alkaline pH, which triggers dissolution.
For ease of use and environmental concerns, the ideal solution (pun intended) is a support material that dissolves quickly in simple tap water.
Designing supports: less is usually more
You should always use enough support to get the job done, but there's no reason to be wasteful. When using a breakaway material, less is definitely more if you want to avoid excessive post-print processing. And designing the minimum required amount of support is good practice for soluble supports too. More support means more printing time, post-processing, and material costs for either approach.
Support material considerations
When choosing a support material, build material compatibility is crucial, whether you're working with a breakaway or a soluble solution.
Thermal compatibility means that both build and support materials have similar print, base, and softening temperatures. Printing at a lower temperature (25°C to 50°C) accounts for most additive manufacturing, if only because soluble support materials capable of withstanding higher temperatures were simply not available until relatively recently.
For example, the temperature and pressure requirements of the autoclave processes used in carbon composite part manufacturing ruled out the use of water-soluble support materials for sacrificial or soluble core use.
Today, there are numerous water-soluble 3D print support options for both low- and higher-temperature printing. Widely used low-temperature support materials include polyvinyl alcohol (PVA) and butanediol vinyl alcohol (BVOH).
Creating a higher-temperature-compatible water-soluble support material, required for use with high-performance engineering thermoplastics like Ultem® (PEI), posed a tough materials-engineering challenge, but it has been solved. Users now have a versatile option available in AquaSys® 180.
Good adhesion is another key consideration when choosing materials. Good adhesion means support material stays in solid contact with the build material. Poor adhesion can mean separation between support and build materials, resulting in loss of detail or print failure.
Support material with wide compatibility is less of a concern if your needs are focused on a single popular print material like PLA. If you work with a wide range of engineering-grade materials, the broader compatibility, better performance, and need for fewer changeouts offered by a premium material like AquaSys® 120 can easily justify the additional cost.

Source: This is taken from the AquaSys 120 white paper.
Working within a closed vs. open system
Material compatibility can get a little complex, and this is one reason for the past dominance of closed systems, where your options were limited but proven to work, as long as you follow manufacturers' recommended pairings.
Today, the market has matured, and a wider range of proven material options and lower costs have given open systems greater momentum.
As the adoption of additive manufacturing continues, it will fuel demand for new options and better-performing alternatives to those on the market today.